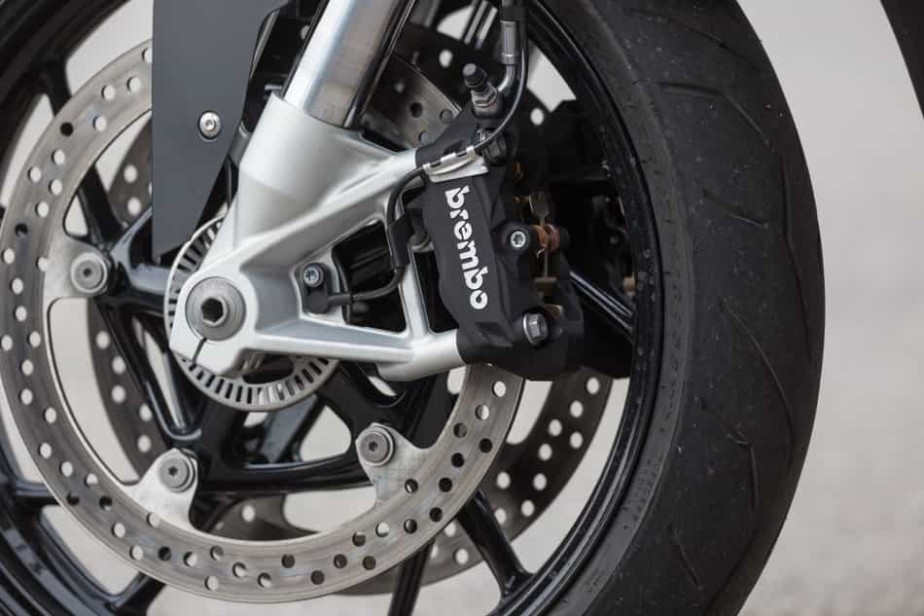
The hydraulic brake system is made of only a couple of main parts, so it is not so difficult to understand how it works. When we push down the brake lever, the brake system makes the motorcycle decelerate. However, have you ever thought about how it actually works?
We will explain how the brake system works in the best way possible, so you don’t need to be an experienced mechanic to understand it.
So how does a motorcycle brake system work? The brake system uses friction to transform kinetic energy ( from an object in motion) to thermal energy (heat). When the rider presses the brake lever, the master cylinder delivers the brake fluid to the calipers, leading to pressure release and squeezing the brake pads to the disc brake.
If you want to learn more about the motorcycle brake system, stay with us because we have more helpful information to share with you.
Table of Contents
How Does a Motorcycle Brake System Work?
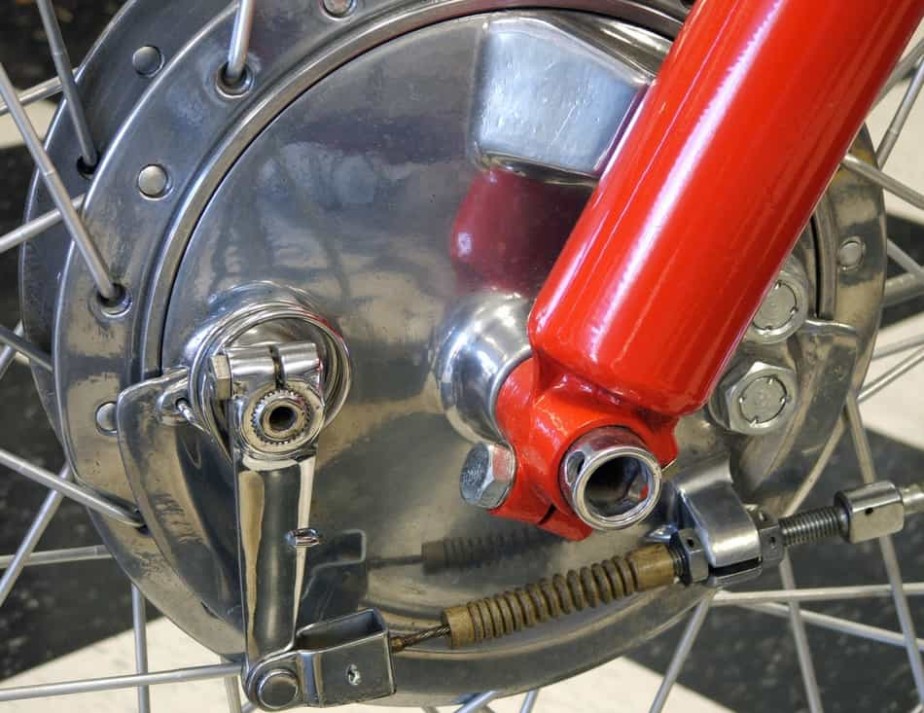
The traditional cable-operated drum brakes can still be found on some motorcycles, but they are being replaced with the hydraulic brake system, also known as the disc brake system.
The brake system shifts kinetic energy to thermal energy. During the time, there has been a lot of improvement in the brake system, so some systems are able to break a motorcycle faster than the latter would accelerate.
It is very simple to realize the hydraulic disc brake system’s basic working concept. The master cylinder pump sends the brake fluid via the brake hoses to the calipers as soon as you squeeze the brake lever.
This results in pressure release, which pushes on the caliper’s pistons with brake pads placed on them. The pads are squeezed onto the disc brake.
Hydraulics Is What It Is All About
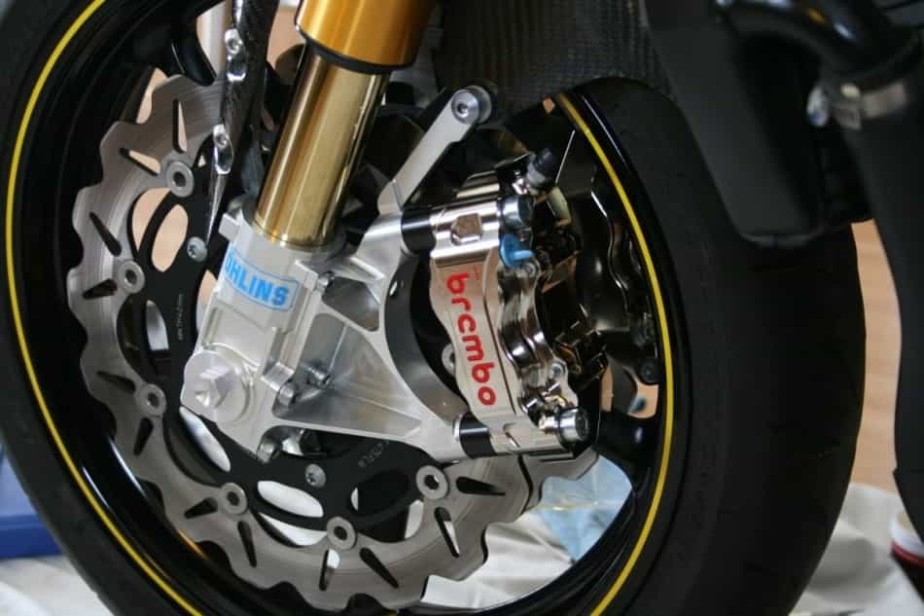
The working principle behind modern motorcycle brakes is shifting force and movement to the lever throughout an incompressible liquid to the caliper pistons, which squeeze brake pads against the disc.
The brake lines must not be dilated, and there can’t be any leaks, nor must the fluid compress so that the force can be successfully shifted. If one of these things happens, you will get soft-feeling brakes, or even worse, no brakes.
So with that being said, let’s take a look at the parts of which a hydraulic brake system is made.
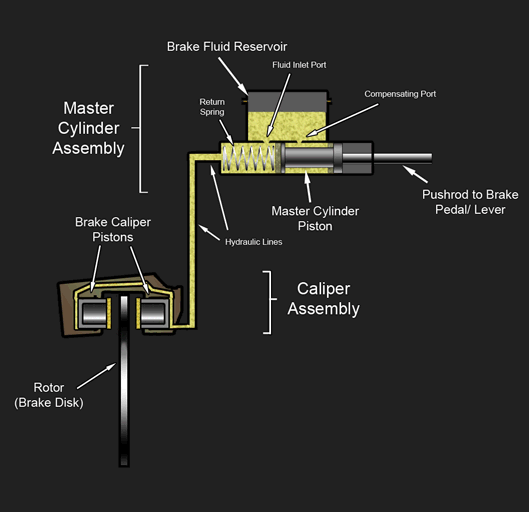
What Is a Hydraulic Brake System Made of?
In this section, we will mention all the parts that make a hydraulic brake system:
Master Cylinder
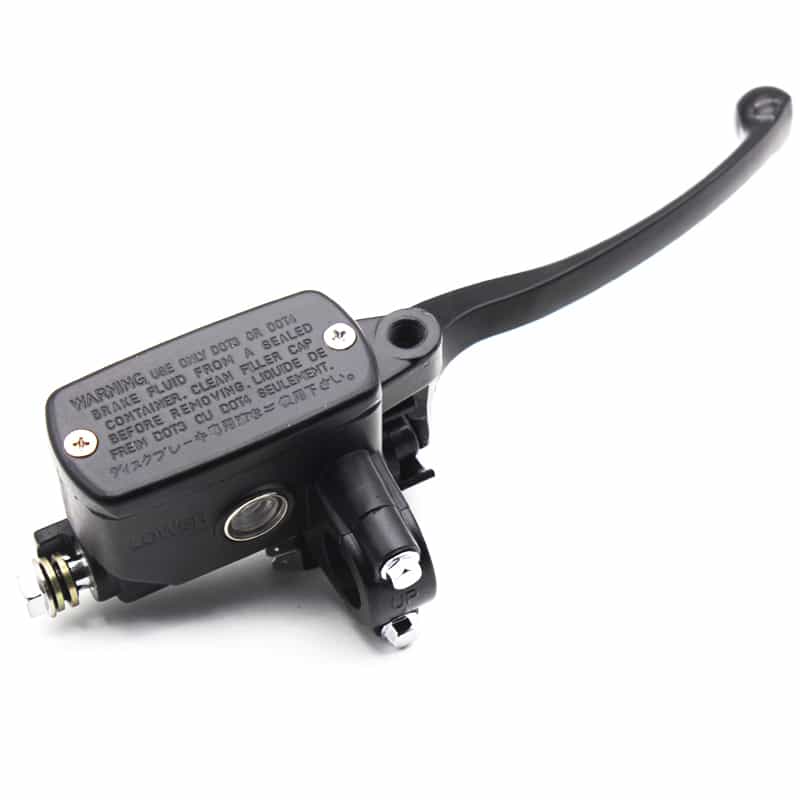
Also known as the “brake pump,” it turns mechanical force into hydraulic pressure every time you push the lever. After that, the brake lever presses on a piston, squeezing the brake fluid.
The force used in pulling the lever is called the leverage ratio, and the size of a master cylinder piston defines the volume of pressure exposed through the system and can happen to go beyond 1,000 kPa.
Brake Hoses
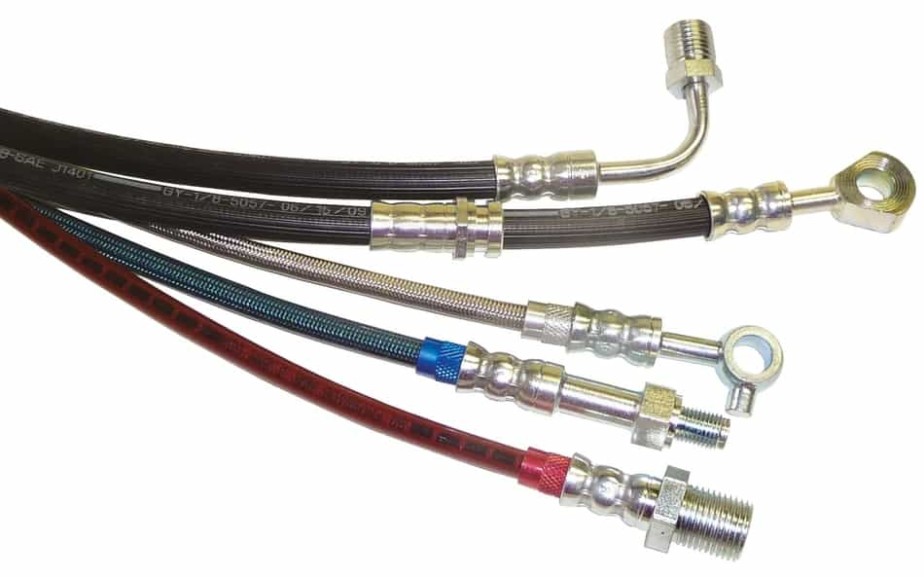
Send pressure from the master cylinder to the calipers. Stainless steel-braided hoses don’t break any stronger, which is opposite to what some may think and believe. They are mostly multilayered, composed of a Teflon inner lining surrounded with Kevlar, stainless-steel reinforcing layer, or braided nylon, and covered in a protective sheathing.
They give you a more consistent feeling when you break as they don’t dilate like rubber hoses do when exposed to hard and intense braking. Rubber hoses should be replaced every four years since they lose their strength as time passes.
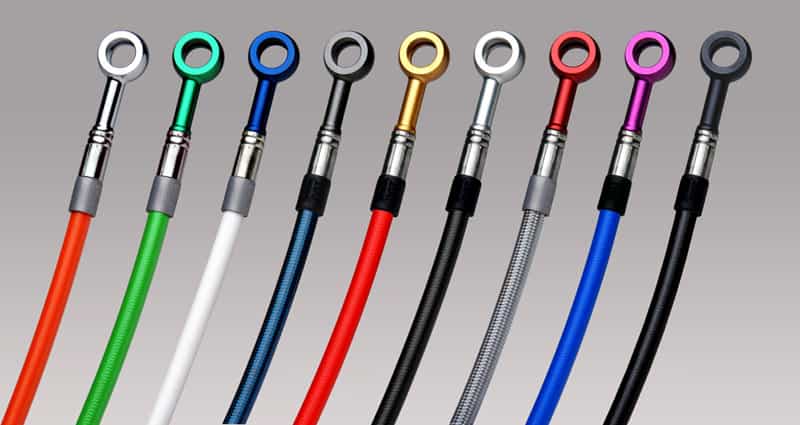
Brake Caliper
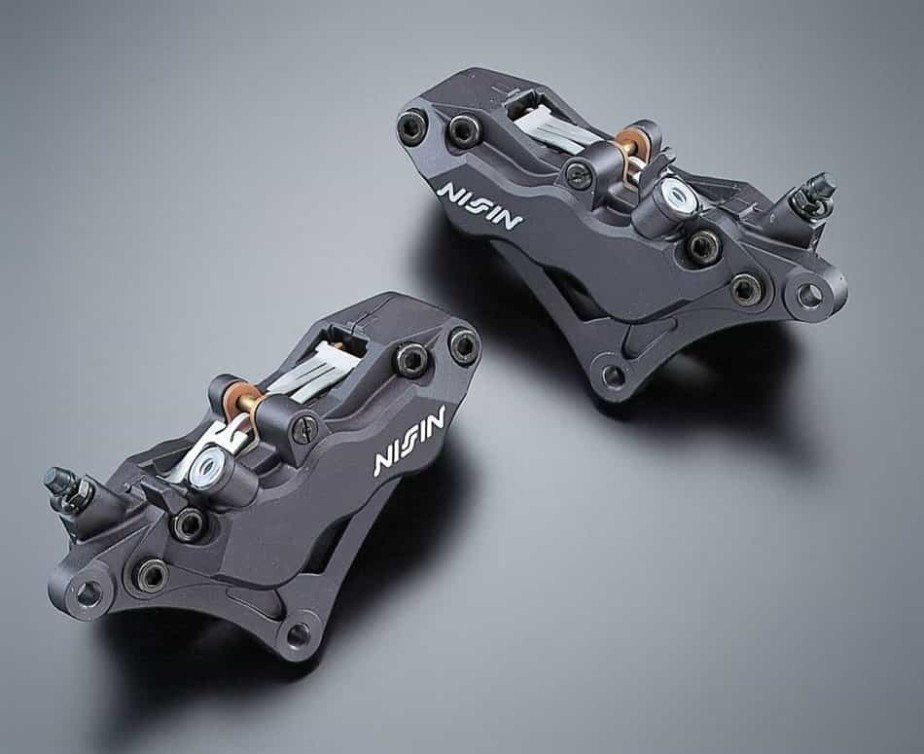
There are two major versions of brake calipers. The first one is called Radial calipers which are a great choice for extreme conditions like racing because of their rigidness. They got their name as they are fastened by bolts that radiate out of the wheel center rather than laterally out of a mounting bracket. For the majority of us, they don’t make any difference.
On the other hand, Monoblock calipers are made of a single piece of metal rather than two combined. This eliminates the small amount of flex among the two halves of a standard caliper and theoretically gives a better feeling, but most of us won’t ride so fast to see the difference.
Brake Pads
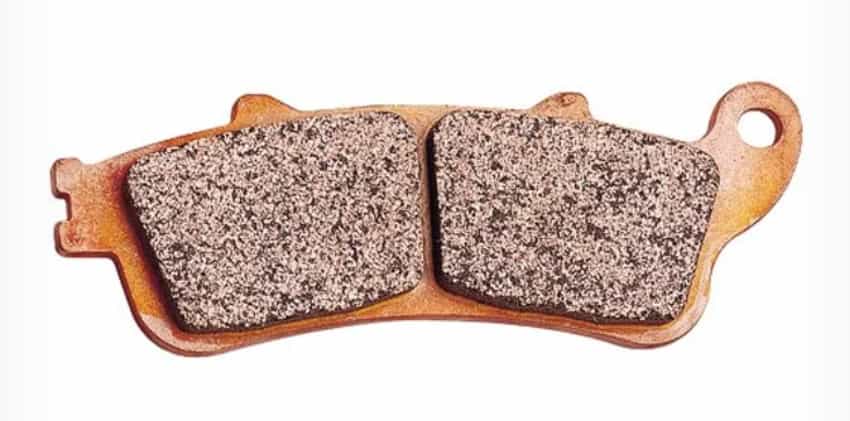
HH pads are the best choice for modern motorcycles since they have the highest coefficient of friction at average temperatures (which the first H stands for) and at temperatures of 350°C (which the second H stands for). The next thing to have in mind is the material from which it is made and how its made.
Organic pads don’t contain any metal. They are low-cost, soft on discs, don’t last very long, and vanish if you hammer them. Also, they are not considered the best option for sports bikes.
Semi-metallic pads are a better option than organic ones since they contain a few metal segments, giving them a higher friction coefficient and greater fade characteristics than organic ones.
We are also going to mention sintered pads. This one is an excellent heat transmitter and has a high friction coefficient. They are considered a great choice, especially if you have a powerful motorcycle. Unfortunately, they might be hard on discs and are high-priced.
Brake Disc
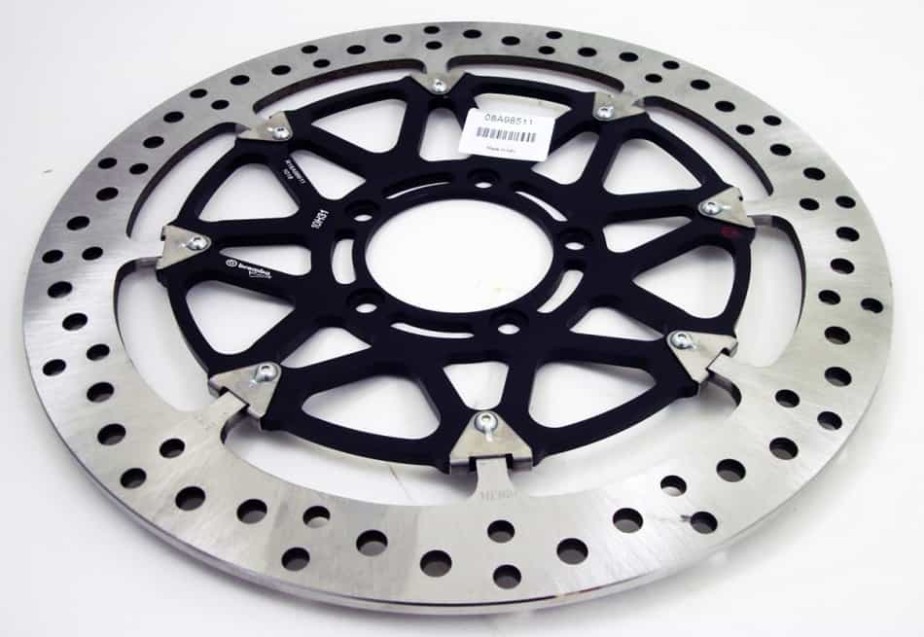
They are often produced out of stainless steel and some iron content, and their function is to transfer the brake pads’ resistance to the wheel contact patch. Today’s discs also contain drilled spots on them to cool the disc faster, along with shedding water and debris.
Brake Fluid
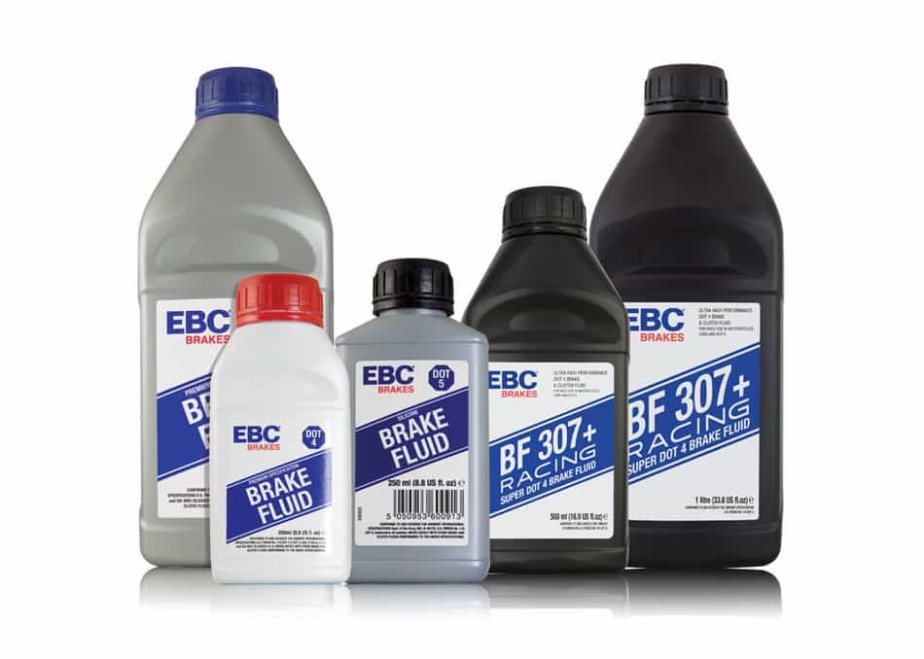
This is not as simple a substance as one could think about. The brake fluid is a liquid substance that shifts force from the brake lever to the brake pads. It needs to be non-compressible to shift the pressure successfully, have low viscosity to work along with ABS components, and have the right lubricity for caliper piston seals and the master cylinder.
Some may forget about the brake fluid since it “just” shifts brake force from a lever to pads. It provides corrosion resistance and has a high boiling point. With that being said, the problem could happen if brake fluid degrades, leading to your brakes fading under hard use.
There are three categories of brake fluid for motorcycles:
- DOT 3
- DOT 4
- DOT 5.1
The numbers relate to viscosity and boiling points. The bigger the DOT number is, the better the brake fluid since it will have a higher boiling point and lower viscosity.
Note: This information is important to have in mind when your brake pads get hot, as you wouldn’t like for fluid to start boiling and become compressible. All these fluids absorb water from the air, and it causes a problem since it lowers their boiling point.
For that reason, it would be smart for you to change your brake fluid every two years and also be aware that all brake fluid bottles are firmly sealed. Every grade labels the fluid’s boiling point out of the heat emission from friction rather than its chemical content. The US Department of Transport (DOT) specifies every grade’s dry and wet boiling points.
The last one is considered completely free of moisture, while it can happen for it to contain 3.7% of water after a year of use.
- DOT 3: 205 oC (dry), 140 oC (wet).
- DOT 4: 230 oC (dry), 155 oC (wet).
- DOT 5.1: 260 oC (dry), 180 oC (wet).
Note: Take a look and see how much performance lowers between dry and wet. This is the biggest reason why brake fluid should be changed every two years. If there is water in the fluid, it will reduce its boiling point, making the brake lever have a spongy feeling and decreasing its braking performance called “brake fade”.
Watch this very interesting video about how a motorcycle brake system works:
Note: Click on this link if you want to learn how to fix your motorcycle brake system.
ABS
The ABS stands for Antiblock Brake System and allows a rider to use the highest braking pressure without locking the wheel. As time passes, the ABS technology has advanced to the phase that it has added functionalities.
The basic concept of ABS is to stop the wheels from locking up when the driver has to use a lot of braking force on a slippery road.
The initial versions were taken from cars. While cars have all of their four wheels on the road and aren’t experiencing large weight shifts, some difficulties were faced when adopted to bike.
But, constant advancement in electronics made it possible for many positive improvements in ABS technology. New ABS systems run almost unnoticeable.
Note: Maximum braking force for any vehicle is a force that applies to the wheels just a moment before it is about to lock. Many factors affect road friction, such as weather and road conditions.
Besides previous factors mentioned, there are also factors regarding tires that affect your braking, such as tire pressure, different tire sizes, tire wear, suspension, cornering, and transfer during acceleration and deceleration. These are scenarios where ABS is of great use.
Speed sensors are mounted above slotted rings on every wheel that measure and compare wheel speed. The signal is transmitted to the ECU (electronic control unit) for observation.
Based on information gathered out of each wheel, the ECU calculates two parameters. The first one is if there is any brake slip, and the second parameter is if the deceleration of one wheel transcends a fixed threshold. These parameters show a locked wheel.
The ECU indicates the hydraulic unit to hold or let go of brake pressure just instantly before reapplying the brake pressure, so it gets the wheel back to the point of the highest braking force just a moment before locking up. Because of this pressure modulation, tires can regain grip, and it gives control and nice steering to the rider.
So we see that ABS gives the rider the ability to use maximum braking force without losing control or locking the wheels.
Interesting Fact: This is one of the reasons why ABS is forbidden from the best racing competitions such as MotoGP or superbikes.
Types of ABS system
ABS 1 (1988)
ABS 1 is the first and oldest one, also known as piston systems. A motor drags back a plunger piston with a spring-tensioned piston to expand the space for brake fluid, successfully decreasing its brake pressure.
ABS 2 (1993)
ABS 2 changed the plunger with an electronically guided friction clutch but even now uses the spring-tensioned piston.
Modern pumps and valve systems use a pump, motor, solenoid inlet, outlet valves, and accumulators. As soon as the system is turned on, the brake fluid is kept in accumulators to release the pressure. A pump sends the fluid back. This is the reason for the pulsation on the foot pedal or brake lever.
24 Hz (Hertz, times per second) is the best ABS systems cycle through this process, and no one is able to match this feat.
As previously mentioned, along with electronics, ABS has gone through some outstanding improvements such as combined braking, dual-channel, cornering, rear lift-up reduction (anti-stoppie), supermoto, and offroad ABS. Traction control depends on the ECU, tire slip signals, and speed sensors.
Final Thoughts
The working principle behind modern motorcycle brakes is shifting force and movement to the lever throughout an incompressible liquid to the caliper pistons, which squeeze brake pads against the disc. The motorcycle brake system is responsible for your safety, and therefore you need to take care of it and maintain it according to your motorcycle manual.
We hope that this article has helped you with some of the basics of the motorcycle brake system.